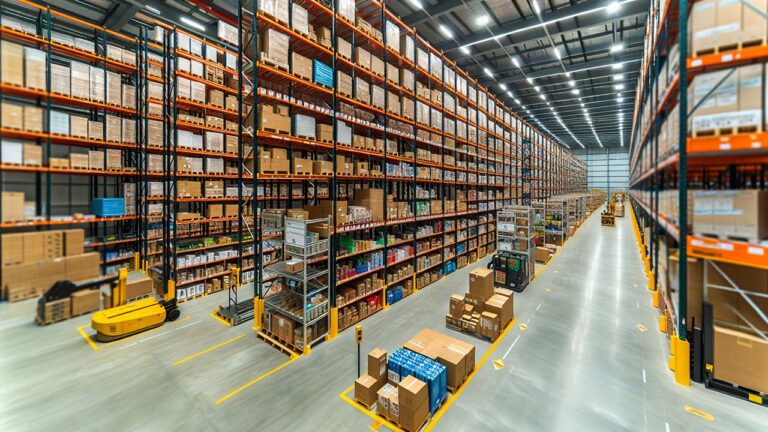
Integrated, Affordable Warehouse Space in Central Texas: Our Central Texas Supply Chain Solutions Provide Integrated Affordable Warehouse Space
Seeking integrated and affordable warehouse space in Central Texas? Our Central Texas supply chain solutions provides integrated, affordable warehouse space with cost-effective warehousing and advanced logistics systems.