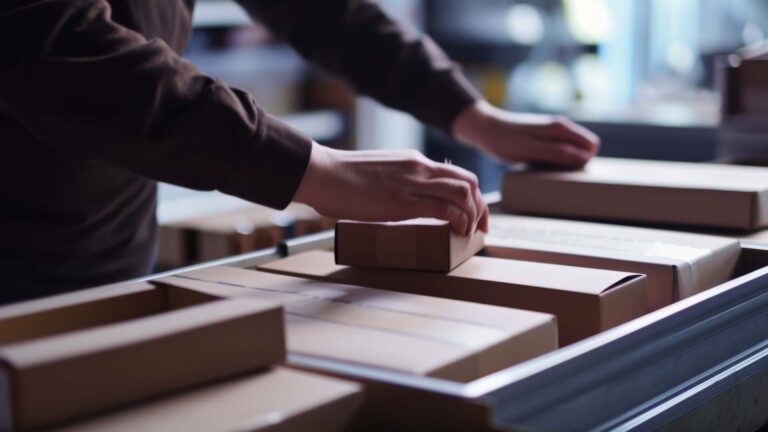
The Power Of Retail Packaging To Deliver Results
Explore the art of retail packaging with our expert insights. Learn to craft retail ready packaging that stands out and supports sustainability with AMS.
Supply chain and business managers constantly seek ways to optimize operations and reduce expenses. A significant area often overlooked is packaging costs. It’s important to consider reducing and optimizing packaging costs as a crucial aspect for any business, especially in the realms of warehousing and distribution.
Warehouse packaging involves the materials and processes used to prepare products for storage and shipment. The cost of packaging a product varies based on several factors.
The packaging price refers to the total cost associated with the packaging of a product. Packaging prices are determined by aspects like weight, size, shape, handling requirements, urgency, and distance of shipment. Understanding these factors is key to optimizing box weights and other packaging expenses.
Packaging optimization refers to the process of modifying packaging methods and materials to reduce packaging expenses while maintaining or improving quality and functionality.
Effective packaging protects products, enhances brand image, and plays a vital role in logistics and supply chain efficiency. Discover how a retail warehouse can help you optimize your product packaging storage and costs.
Several factors can inadvertently increase packaging cost:
When storage areas and packing lines are not optimally designed, it results in inefficient workflows. This inefficiency can cause delays and increased labor costs.
The longer it takes to pack an item, the higher the labor costs associated with it. Extended packing times can be due to several factors such as inefficient packing processes, inadequate training of staff, or the complexity of the packing requirements.
If the packing materials used are not durable or suitable for the products, they may break or fail during transit. This can lead to the need for repacking with better materials and potential product damage, both of which incur additional costs.
Manufacturing processes that do not consider the packing stage can lead to the production of items in shapes or sizes that are not packaging-friendly. This misalignment often results in the use of more packaging material than necessary or the need for custom packaging solutions.
When the packaging size significantly exceeds the size of the product, it results in wastage of packing materials and increased shipping costs due to the larger volume, even though the product itself might be small or lightweight.
Optimal packing involves using the right size and type of materials, as well as effective packing methods. Missing out on these optimizations means higher costs due to the use of more materials than necessary, increased shipping expenses, and a higher risk of product damage.
Ineffective packaging often leads to heavier or bulkier parcels, which can significantly increase shipping costs.
Efficient use of warehouse space is crucial for cost-effective operations. Poorly organized or cluttered warehouses can lead to difficulties in locating goods, which slows down the packing process. This inefficiency not only increases labor costs but can also result in the need for additional warehouse space, which is an added warehouse cost.
Evaluating your current packaging methods and materials is the first step towards optimization, identifying areas where packaging costs can be reduced without compromising quality. Learn how our warehousing services can help you cut down on packaging costs.
Reducing packaging cost is pivotal for enhancing a company’s profitability and operational efficiency. These practical strategies can streamline processes and significantly cut down on expenses.
Implementing a standard set of packaging sizes and materials can significantly streamline the packaging process. It reduces complexity, enables bulk purchasing of materials at lower costs, and simplifies inventory management.
Lighter and smaller packaging not only reduces material costs but also lowers shipping costs.
While standardization is beneficial, for certain products, custom-sized packaging can reduce waste and costs.
Investing in more durable packaging materials can reduce the frequency of damaged goods and returns, ultimately saving costs associated with replacements and customer dissatisfaction.
Implementing automated packing processes can speed up the packing time, reduce labor costs, and minimize human error.
Streamlining the assembly and packing process, possibly through layout optimization or better training, can reduce the time and labor involved in packaging, thereby lowering costs.
Kitting, or the process of grouping multiple items into a single package for shipment, can reduce handling and processing time, thereby lowering costs.
Packaging innovations, especially those focusing on sustainability, can not only reduce costs in the long term but also appeal to environmentally conscious consumers.
By using smaller boxes that fit the products more snugly, companies can reduce the amount of packing material needed, lower shipping costs due to reduced volume, and minimize the environmental impact.
Eliminating or reducing unnecessary packaging components can significantly cut down on material costs and waste.
Packaging that serves multiple purposes, such as reusable or returnable packaging, can offer cost savings over time. This approach is particularly effective in closed-loop supply chains or with products that require return or reuse.
Using packaging appropriate to the product’s durability can save costs. Fragile items may need more protective packaging, while more durable items can be shipped with less packaging, saving material costs.
Ensuring that products are properly packaged to withstand transportation and handling can reduce the rate of returns due to damage.
Building a strong relationship with a single supplier can lead to cost savings through bulk discounts, better negotiation terms, and streamlined supply chain management. Learn how to optimize and reduce your packaging costs with our advanced warehouse services.
3PL providers, with their expertise in warehouse management and logistics, can play a pivotal role in helping businesses optimize their packaging cost. From providing integrated warehousing solutions to leveraging advanced 3PL software, these providers offer a range of services that can significantly reduce packaging prices.
Inefficient packaging practices can lead to increased costs and reduced profitability. By implementing the strategies outlined, businesses can optimize their packaging processes, leading to significant packaging cost savings. Embrace these practices to ensure your packaging is as cost-effective as possible.
Discover how our fulfillment services can enhance your packaging efficiency, helping you save costs and improve your bottom line.
Explore the art of retail packaging with our expert insights. Learn to craft retail ready packaging that stands out and supports sustainability with AMS.
Explore the process, importance, benefits, fulfillment options, cost considerations, and tips for designing custom packaging.
Your fulfillment pick rate can help grow or hinder your business. Here are 12 tips for how to pick faster in a warehouse operation.
There was a time when businesses revolved centrally around the customer and their needs. Decisions were made based on what is best for the customer first. People did what they said they would, and jobs were completed on time. AMS carries on the tradition of customer service today.
AMS is a customer service-centric warehousing and fulfillment company. We have the software, but we don’t replace PEOPLE and SERVICE with software. Being that we are a contract manufacturer as well, we have a lot of expertise and capability that you can rely on and trust.