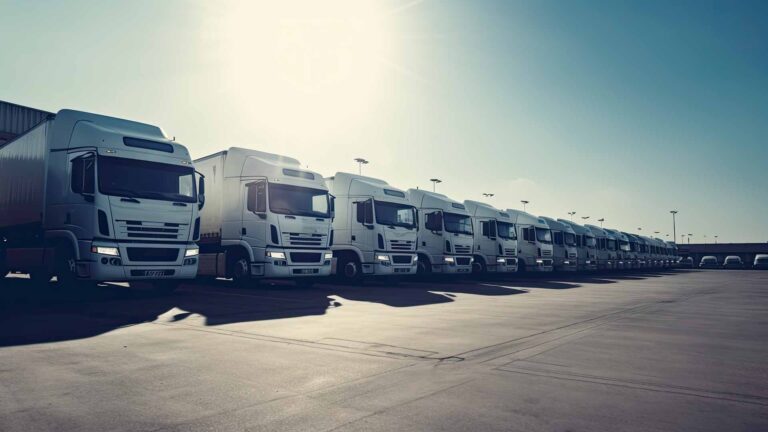
Basic Guide to 3PL (Third Party Logistics)
3PLs provide flexible and scalable logistics solutions can grow with your business. But what is a 3PL and how do they work?
In order to keep up with the modern, fast-paced world, it is essential that warehouses are running efficiently for both customer satisfaction and financial success. This blog post will discuss numerous tactics and technologies which can be put in place to streamline warehouse operations as well as optimize layout and inventory management systems, ultimately contributing towards an efficient warehouse environment. So here we dive into how exactly one could establish a smooth-running facility!
TLDR? Article Summary
Creating an effective warehouse begins with a carefully planned layout. This is key to achieving maximum utilization of the space available while improving workflow, which in turn boosts productivity and keeps operational costs low. For this reason, it’s essential that good housekeeping practices are observed so as to ensure accessibility for frequently retrieved items, plus there must be consistency when storing goods within the facility.
Making use of vertical racks, containers and mezzanines will assist in optimizing space whilst streamlining processes – two steps towards setting up an efficient warehouse complete with performance-boosting tips! Applying these guidelines should help get you well on your way toward realizing such goals.
Maximizing usage of warehouse space is necessary for enhancing efficiency. This can be done by arranging items according to SKU, product type or other traits which helps optimize the area and streamline activities. To minimize labor costs while also increasing storage density, one solution would be utilizing a Pallet Shuttle system that eliminates manual handling operations. Through judiciously using various warehouse solutions, it’s possible to not only augment productivity but also capitalize on available resources in your warehouses effectively thereby boosting their effectiveness overall.
Maximizing warehouse efficiency is a critical step in improving operations. The process involves assessing and adjusting existing protocols to cut down on costs, guarantee precision and maximize productivity. One way this can be accomplished is through cross-docking, which shortens storage time by shipping merchandise out soon after their arrival at the facility. Utilizing multi-carrier shipping software also facilitates dispatch duties by creating precise labels for carriers as well as delivery documents associated with each shipment order.
The key to a successful warehouse operation is having an effective inventory management system. Streamlining this process can be achieved by utilizing warehouse management software, cyclic counting, and forecasting needs. By using modern warehousing software you are able to effectively oversee products, execute the necessary steps for procurement and make anticipatory preparations.
This information in real-time helps with optimizing pick/pack performance along with keeping track of warehouse efficiency plus supervising different components of your organization’s warehouses so as to upgrade coordination while at the same time improving overall effectiveness within operations there too.
Warehouses have the potential to increase efficiency, and that’s where a Warehouse Management System (WMS) comes in. It can help optimize warehouse space by evaluating SKU demand and stocking them accordingly for optimal productivity. This system also enables routes to be optimized when it comes to picking orders or putting items away into storage. Cloud-based WMs offer real-time analytics you can access easily from any secure location.
A necessary part of inventory management is cycle counting, which involves doing frequent counts and recording discrepancies to make sure that stock levels are correct. This method can be more cost-effective than others for maintaining steady accuracy in record keeping. Commonly, warehouses will perform a count every week or month, with the entire collection being accounted for at least once during a 3 month span.
In order to guarantee accurate and timely inventory handling training must be given as well as accurately documenting the process of cycling through counts. By implementing these practices you’ll have great assurance your stocks records stay precise and reliable information about product availability is recorded correctly.
Demand forecasting is essential to ensure an optimal level of inventory management, production planning and supply chain operations. It involves collecting historical sales information, spotting trends or patterns and employing predictive analytics for coming up with a forecast. By incorporating the technique into warehouse activities it will give you the capacity to enhance efficiency as well as prepare your business for expected future demands more adequately.
For effective demand forecasting, businesses should be gathering data from their past sales history in order to make informed decisions about stocking levels and alterations within their supply chain operation processes.
Warehouse efficiency can be enhanced by introducing tactics such as batch picking, zone picking, and technologies to improve the picking and packing processes. By adopting appropriate techniques while taking advantage of cutting-edge technologies, it is possible to reduce labor costs while simultaneously enhancing fulfillment performance in your warehouse.
In this section we will explore several approaches and technological tools that may boost efficacy when dealing with warehousing operations concerning pick & pack activities.
Batch picking is a beneficial method for organizing many orders into small batches. From 8 to 16 years old. This tactic results in an efficient pick path and keeps order-pickers away from visiting the same item spot multiple times while completing numerous orders. The application of batch picking facilitates the process of selecting products as well as diminishing its stages which leads to boosting efficiency at warehouses all around. Good organization and collaboration are essential when utilizing this technique since it secures accuracy along with effectiveness during warehouse processes.
Organizing the warehouse into distinct zones based on item types can be an effective way to pick orders, boost efficiency and reduce mistakes. To use this picking method effectively, staff should be assigned each zone and trained accordingly. Monitoring of operations within these separate areas is necessary for maintaining maximum results in terms of streamlining processes and improving overall warehouse efficiency. Zone picking has demonstrated itself as a powerful tool that not only cuts down time but also minimizes walking distances among workers involved in order selection activities.
Warehouse efficiency can be significantly improved through automation technology, which automates processes such as inventory control, order completion and shipment. Real-time information regarding product status and location is provided by automated guided vehicles (AGVs), robots and sensors thus allowing for higher precision and production capacity.
By investing in these technologies it becomes possible to decrease picking time while increasing warehousing output since goods are delivered to the pickers instead of requiring them to go retrieve items themselves. Optimization of logistics operations helps lower costs too, so warehouse efficiency ultimately benefits from this investment.
Warehouses can be more efficient and productive when they have employees with the right training and incentives. By having comprehensive employee training programs, errors in warehouse operations may decrease while executing logistics processes could become faster. Incentive pay is also an effective strategy that boosts labor productivity by encouraging workers to work harder and better. Here we will explore various techniques for developing successful employee training plans as well as offering attractive incentive packages within a warehouse environment.
Ensuring that all warehouse operations are running smoothly and efficiently is achievable through comprehensive training for the employees. By providing ongoing instruction covering every aspect of their roles, it will ensure workers stay up to date with changes or new practices within the organization. Cross-training personnel in multiple duties can be a challenge. Help boost productivity by making them well equipped to handle tasks without any issues. With a sound training program implemented correctly, your warehouse staff would be properly prepared to perform their obligations proficiently and productively.
Incentive programs are essential for inspiring warehouse workers and elevating productivity. Different types of incentives, such as incentive pay or recognition/reward schemes, can be effective in motivating employees to give their best effort. Additional ways to incentivize staff might include offering monetary rewards when objectives are met, granting flexible scheduling options, and applauding excellence by praising warehouse personnel for superior performance. By utilizing successful encouragement systems one can create an enthusiastic and productive warehouse team.
Maintaining safety in the warehouse is important for operational efficiency. Not only does it provide a secure environment for personnel, but also helps to raise productivity.
Awareness and enforcement of proper safety guidelines should be at the top of any priority list when running a successful facility. Through these measures, you can ensure that your warehouse runs safely and efficiently without added risks or disturbances to day-to-day operations.
Warehouse workers can benefit greatly from safety training courses. Such programs provide personnel with the right knowledge to take action in emergencies and promote a more efficient warehouse environment as well as reduce any potential risks. The comprehensive training includes general, risk-specific, and task-specific techniques that enable employees to work safely within their workspace. By providing proper instruction on security protocols, you are making sure your staff is always prepared for unexpected incidents at the warehouse without compromising efficiency or productivity levels of operations.
To ensure the safety and effectiveness of warehouse operations, it is important to maintain equipment in good working condition. An effective preventive maintenance plan can help limit downtime due to unexpected malfunctioning and prolong the lifespan of machines used within warehouses. Through regular inspections that identify any potential problems before they become serious, expensive repairs or long-term unavailability of resources can be prevented while maintaining efficient functioning simultaneously.
Establishing scheduled maintenance sessions along with appropriate corrective measures when necessary will guarantee your warehouse has its tools running safely as well as productively at all times.
To ensure an efficient warehouse operation, it is important to maintain a smooth receiving process. Working together with suppliers can improve the procurement of products and services, ultimately leading to more reliable supply chains. To make sure there is effective collaboration with vendors for increased efficiency in the warehouse environment, careful planning and adjustable staffing should be implemented as part of your warehouse strategy.
This article examines how collaborating effectively with providers results in enhanced efficacy within warehouse operations around acquiring goods from them properly while adhering to good warehousing techniques that are safe yet optimized overall.
By planning ahead in warehouse management, it is possible to maximize supply chain and production systems. Through close collaboration with suppliers for the exact time of arrival and number of items received, a manager can make arrangements for storage space as well as ensure sufficient resources are available so that goods can be processed efficiently for sale.
Advance knowledge concerning incoming shipments allows warehouse managers to handle them quickly thus improving overall efficiency within the facility itself.
Having a flexible staffing plan is critical for maintaining an effective and efficient warehouse. This approach provides businesses the ability to adapt their labor force according to fluctuations in demand, allowing them to increase personnel when significant shipments arrive. Having such an arrangement allows you to maximize stocking and receiving of merchandise which will ultimately aid with optimizing your warehouses’ efficiency levels. By utilizing this practice, organizations can ensure they keep up smooth operations within their facility while also driving improved results from it.
In order to stay competitive in today’s market, businesses need to integrate the latest “smart warehouse” technologies into their warehouse operations. Advanced solutions such as AI and machine learning along with IoT applications can boost efficiency while streamlining processes within the warehouse. Automation of tasks, real-time product tracking information and cost savings are only a few benefits these cutting edge systems bring about when implemented properly, which will help reduce errors on top of improving overall efficiency.
Integrating new tech into your existing infrastructure is crucial for any company looking for success – regardless if it be large or small scale operations inside a single facility or multiple locations around different parts of the country/world. All benefitting from improved productivity thanks to more efficient utilization at warehouses across them all!
The integration of AI and machine learning into warehouse management systems are transforming the way warehouses conduct operations. By taking advantage of this technological advancement, managers can use warehouse management software to more accurately track stock movements as well as product storage and retrieval all while minimizing any potential errors in order preparation. This combination enables organizations to optimize their processes and maximize efficiency by streamlining various warehouse tasks throughout the company’s entire operation.
Warehouse efficiency can be substantially improved through the use of IoT solutions. With automated tasks such as inventory control, shipping and order completion getting a boost from real-time data provided by robots, sensors and automatic guided vehicles (AGV’s), an investment into these technologies provides greater logistics processes accuracy with warehouse productivity gains. The information collected on item locations yields valuable insight that aids in streamlining operations at any given warehouse.
To maintain your competitive edge and meet customer demands, it is essential to optimize the efficiency of your warehouse. Utilizing advanced technologies alongside strategies such as improving warehouse layout for increased productivity, streamlining inventory management operations, enhancing picking and packing processes, providing sufficient training to employees with incentives, focusing on safety in the workplace, and collaborating with suppliers, all these will help take Warehouse performance up a notch!
Need help figuring out the total volume of usable space in your warehouse? We built a simple tool to help you calculate that.
The pallet storage capacity calculator quickly determines the total number of pallets your warehouse can store based on rack configuration.
Creating an efficient warehouse management system requires careful planning. This includes arranging the layout in a way that optimizes space, keeping up-to-date on technology advancements, utilizing suitable containers and pallets for items being stored within the facility, educating personnel about safe procedures and protocols as well as taking security steps to protect inventory from theft or damage.
When these measures are implemented correctly, it will lead to running a successful and effective warehouse management plan with ease.
To enhance warehouse efficiency, it is key to select the proper frontline supervisor, apply technology, maximize space utilization and arrange each workstation. Coming up with a storage plan can help in achieving better results as well. Plus, you should always be open for new ideas. Improvements of methods. Following these procedures will ensure that your warehouse reaches optimum efficiency quickly and effectively.
An efficient warehouse utilizes current technology, appropriate storage solutions and automated procedures to increase productivity. Quality personnel are vital for the smooth running of such warehouses while modern inventory management systems coupled with well-organized items in their designated places all help build an effective warehousing operation.
By organizing and making the most of your warehouse, you can boost productivity. This involves planning a strategically-thoughtful layout, having set standards for operational processes, eliminating mess through organization techniques, maximizing available storage space as much as possible, and relying on technology to bring about optimal operations.
In order to ensure peak efficiency of their warehouse, companies must utilize certain techniques like evaluating performance and designing a practical layout. They should look ahead in terms of forecasting as well as keep track of products while taking advantage of available technology.
Proper staff training is essential for achieving successful outcomes from warehouse operations. By keeping these strategies in mind and following through with them accordingly, businesses can optimize their efficient warehouses effectively maximizing resources at hand.
3PLs provide flexible and scalable logistics solutions can grow with your business. But what is a 3PL and how do they work?
This warehouse management article helps you understand practical advice for any business that is involved in running warehousing operations.
What is a fulfillment center and how does it differ from a distribution center? How do I decide which is right for my business?
There was a time when businesses revolved centrally around the customer and their needs. Decisions were made based on what is best for the customer first. People did what they said they would, and jobs were completed on time. AMS carries on the tradition of customer service today.
AMS is a customer service-centric warehousing and fulfillment company. We have the software, but we don’t replace PEOPLE and SERVICE with software. Being that we are a contract manufacturer as well, we have a lot of expertise and capability that you can rely on and trust.