Consistent levels of high quality.
At under 0.01% NCMR, our quality is proven top notch. Because of our strict adherence to your spec, you can rest assured that your product will be free from time consuming reworks.
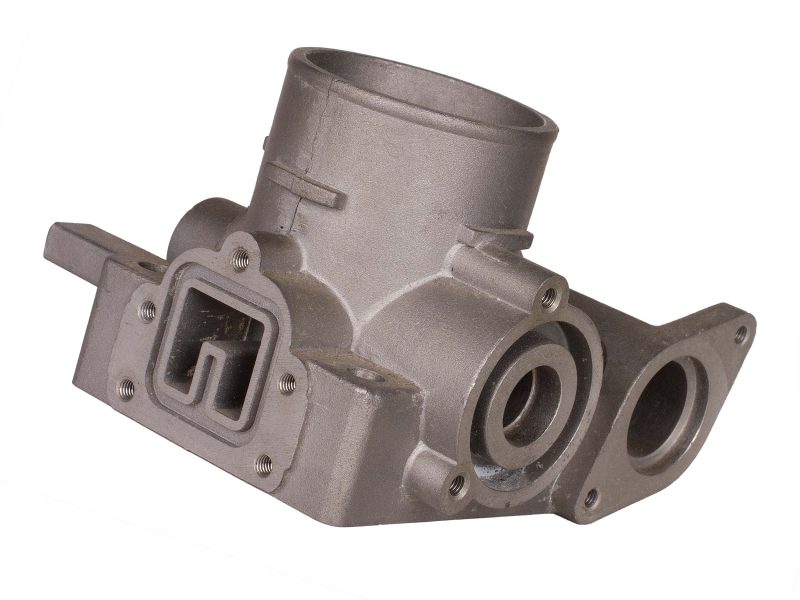
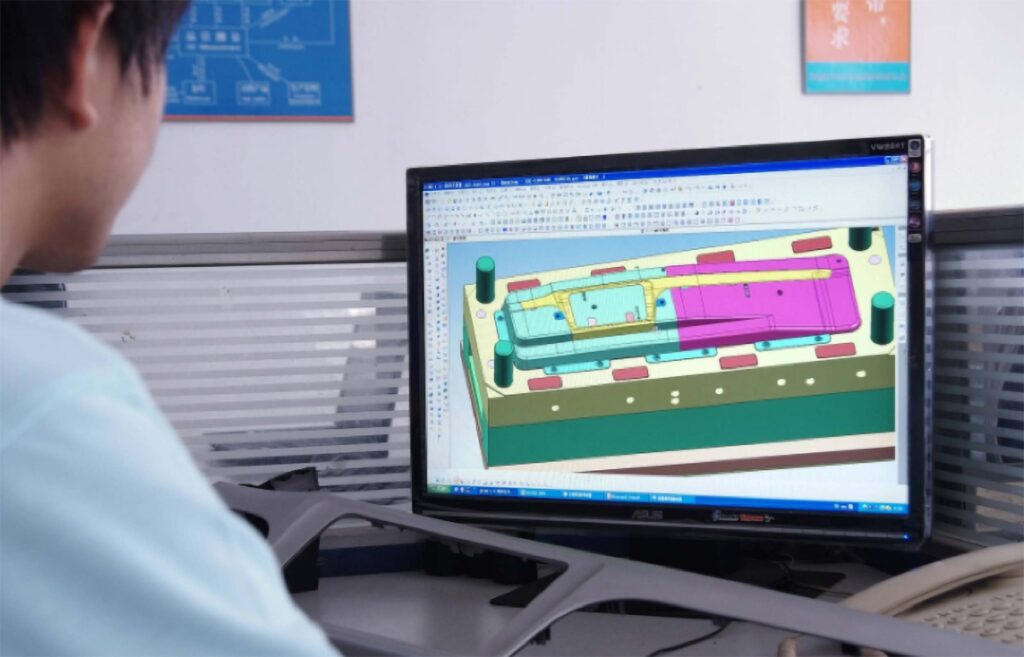
Robust and detailed FEA process.
Our prototyping process involves highly detailed percentage based tolerance checks. This gives you a clear indication of how close each piece and part falls within your manufacturing spec.
Since 2012, we have created a reputation for solving manufacturing quality and supply chain issues.
How we achieve quality
Contract Manufacturing Quality
Our proactive approach defines success by how closely we match the specification provided to us, and our focus on manufacturability.
- ISO 9001 - 2008
- ISO/TS 16949 - 2009
- ISO 14001 - 2004
- OHSAS 18001
A quality process that has proven results through years of refinement.
Initial Design Goals
Over 1-2 meetings, we will complete our understanding of your design goals. This will include information such as BOM, battery & PCB requirements, material finishes, and others.
Kick Off DFM
We will study your designs and begin providing engineering design suggestions to improve manufacturability. This can take 2-3 weeks, maybe longer for more complex products.
Production Estimate
At times, sub-assembly can be much more cost effective saving both assembly time and shipping costs. This process can be as simple as applying specified labeling to near complete mechanical assembly processes.
Prototyping
This begins the engineering prototyping & design review process. The time this requires can be more accurately estimated after completing the DFM feedback.
Finalize Design
Once prototypes are approved, and design files locked, AMS provides a final design file which includes material color, surface finish, tolerance, assembly requirements, etc. This file can be used to kick off tooling for mass production.
Tooling & Production
Most commonly performed at the final step of manufacturing, functional testing ensures that product specifications are met and the mechanics of the product are performing as desired.
Free Resource
What is poor quality actually costing you?
Poor quality costs a lot, but do you know the full extent to those costs? In this free resource we detail ways in which the hidden costs of quality can permeate and hamstring companies.
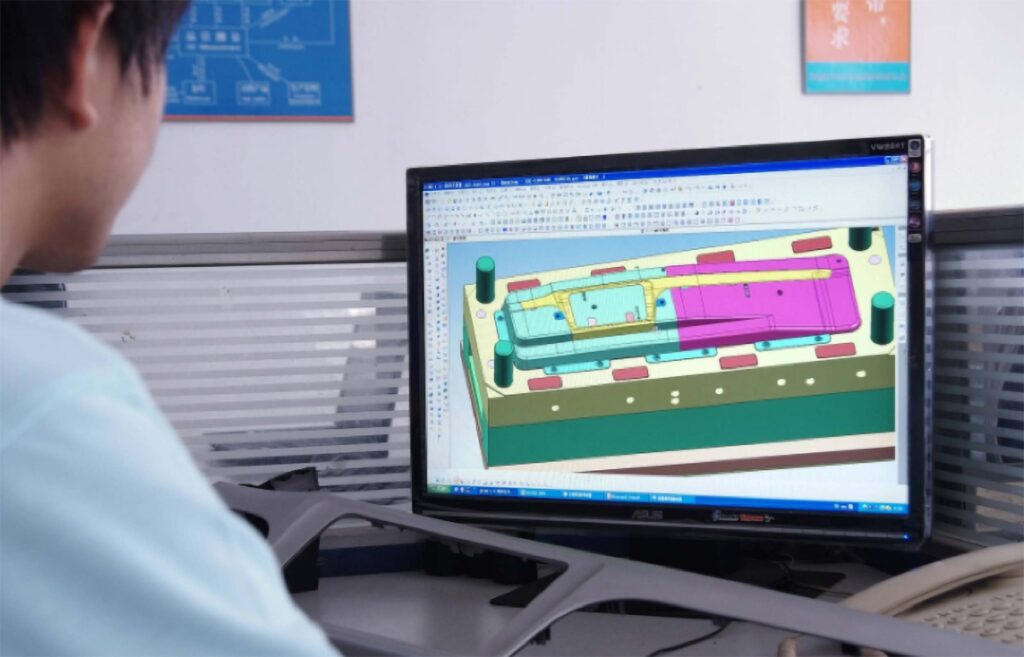
Why Quality Control Does Not Necessarily Improve Quality
July 3, 2020
Quality is a hot-button issue in manufacturing. That’s because many companies understand that poor quality carries with it great cost. However, even though this understanding generally exists, most companies are unaware of the true cost of poor quality.
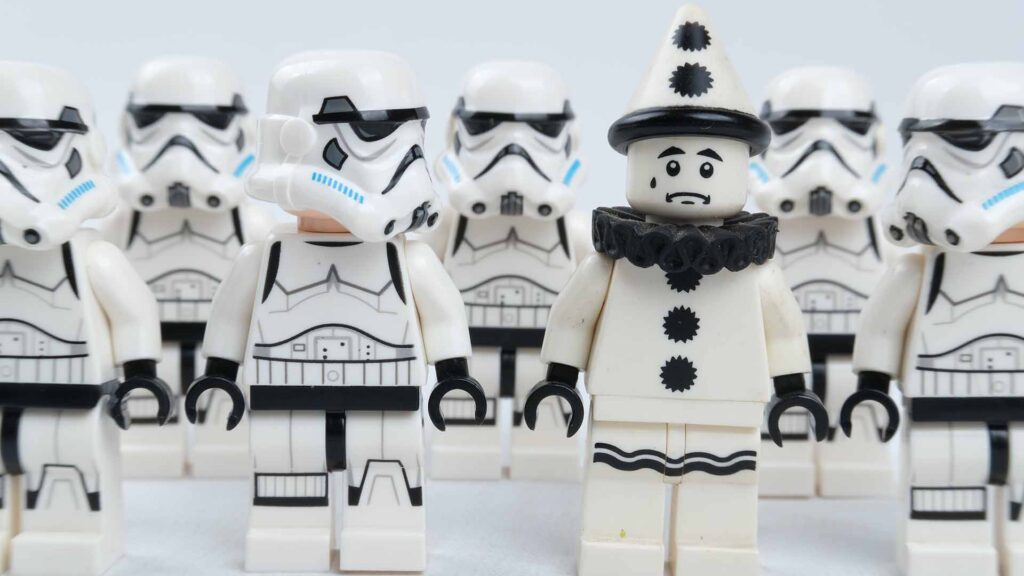
Non-Conformance in Manufacturing and How to Stop It
Sept 9, 2022
Non-conformance in manufacturing processes can cause issues including increased costs. But what is nonconformance and how do you correct it?
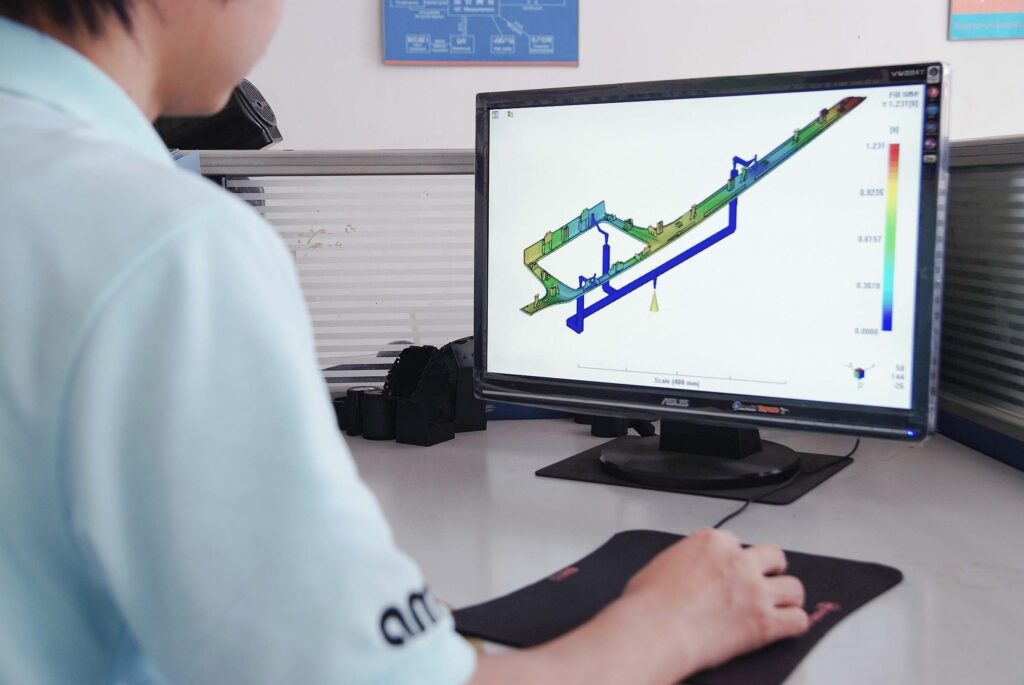
How DFM Can Dramatically Cut Product Costs and Increase Quality
June 18, 2020
The engineering work of DFM or Design for Manufacturing is the practice of designing a product so that is able to be efficiently manufactured. It is set apart from traditional functional engineering which seeks to achieve a desired mechanical or visual design.